Bridge deck inspections are a significant component for many DOTs or the firms they employ for that purpose. And there are over 610,000 highway bridges in the United States, and most of these bridges’ construction, repair, rehabilitation, and inspections are funded by the Federal Highway Administration (FHWA).
Responsibility for the regular inspection of these highway bridges, according to the U.S. Department of Transportation (DOT), is divided between each State and the federal government,
“The State transportation department (State DOT) must inspect, or cause to be inspected, all highway bridges on public roads that are fully or partially located within the State’s boundaries, except for bridges owned by Federal agencies. Federal agencies perform inspections through other processes beyond those performed by the State DOTs.”
And in several states, most county and city bridges are inspected by their individual owners.
Of course, five basic types of bridge inspections are required for highway bridges. These are the initial inspection, as well as in-depth damage and special inspections. Then there are the routine inspections.
As the U.S. DOT explains, these “routine” inspections are the most common type of inspections performed and are generally required every two years. A “routine” inspection aims to determine a bridge’s physical and functional condition on a regularly scheduled basis.
And this includes the bridge deck.
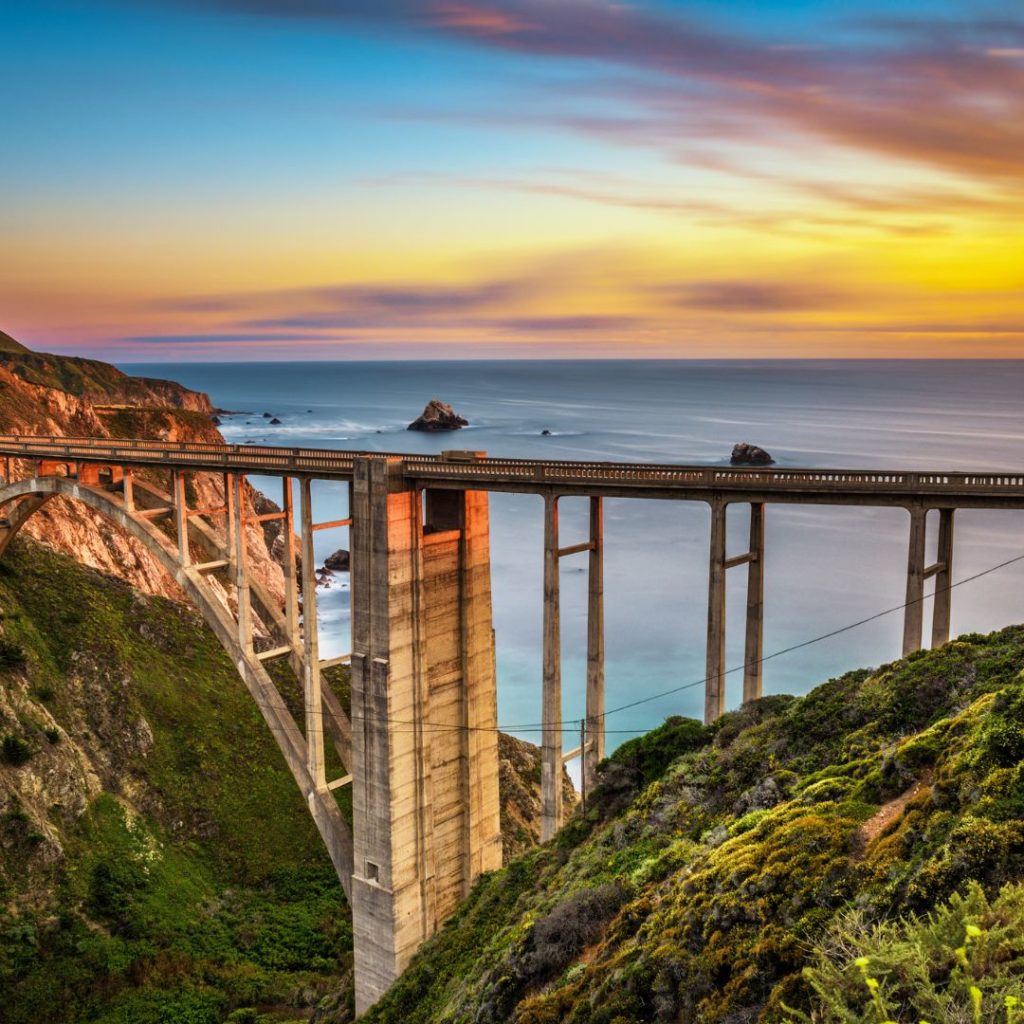
Considering the Importance of the Bridge Deck Inspections on Highway Bridges
Perhaps it goes without saying, but almost every component and part of a bridge are critical to its integrity and ability to support the load it was designed to carry. And routine bridge inspections usually encompass, at minimum, both visual observations and hands-on measurements of all the major areas of a bridge structure.
The primary purpose of a routine inspection is to determine a bridge’s physical and functional condition, identify any changes that have occurred since the last inspection, and ensure that the bridge is structurally sound, safe, and meets the minimum service requirements.
When it comes to the bridge deck, there are particular concerns that inspectors must take into consideration.
Bridge Decks: The Vital Roadway
The main part of a highway bridge is typically referred to as the superstructure, and it is the superstructure that bears the weight of the load as it passes through the bridge. The superstructure is comprised of the deck slab or decking, as well as the girders and trusses. However, the specific components will vary based on the type of bridge and the material the bridge is constructed of, such as steel or concrete.
The bridge deck, or decking, not only holds the load weight but also helps transmit the weight and pressure below bridge substructures. Only bridges that are 20 feet or more in total span length are required by the FHWA to be load rated.
The most visible – and exposed – portion of a bridge deck is the roadway and sometimes the pedestrian walkway, the surface of a bridge. And as an article at Science Direct points out,
“Bridge decks are vulnerable, subject to attack by water and chloride that can lead to deterioration and issues with longevity and durability of the bridge decks. The installation of an effective waterproofing membrane is, therefore, an essential part of the bridge deck system in addition to the drainage system.”
In addition, on steel bridge decks, the asphalt pavement that is laid on the top of the main girder, or longitudinal stiffener, is particularly vulnerable to cracks. Interconnection parts of the bridge deck, such as expansion joints, can be subject to undue exposure to the elements, which can lead to deterioration issues.
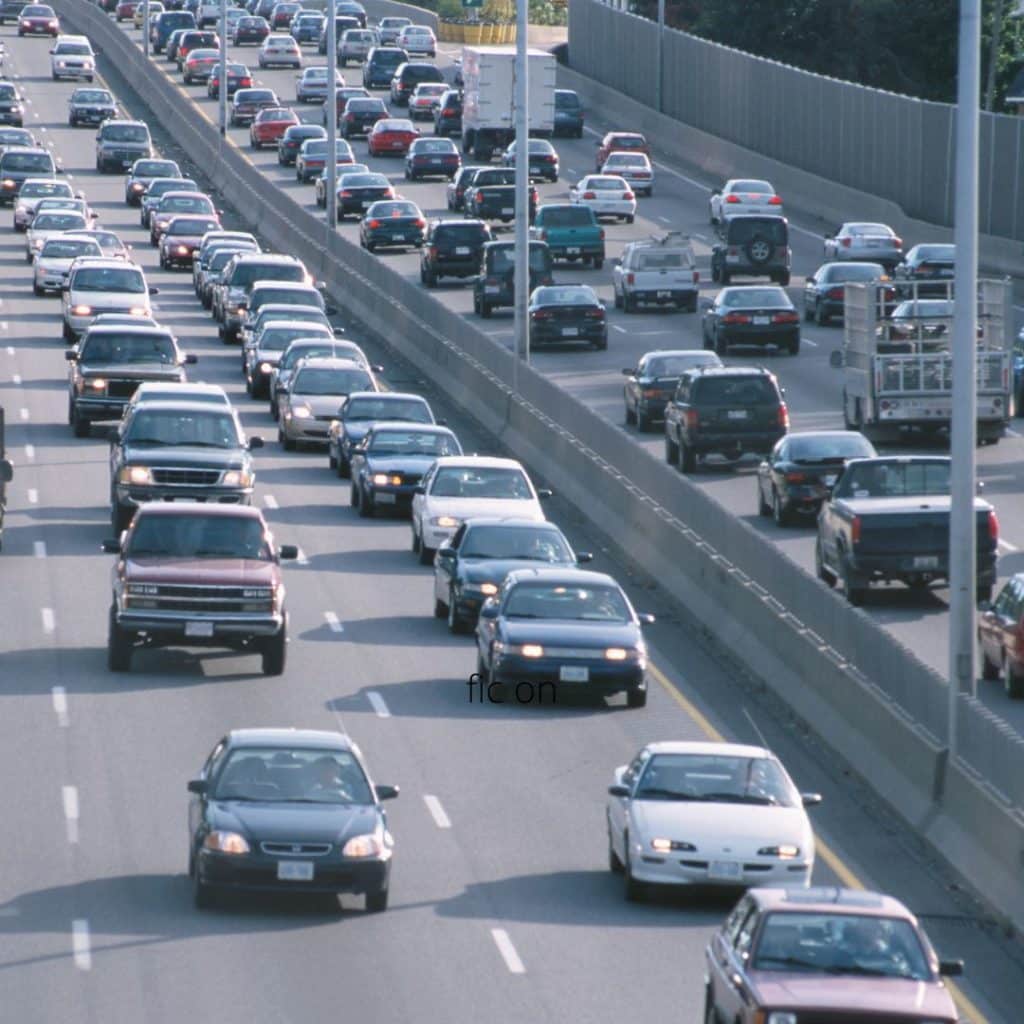
Bridge Deck Inspections: An Overview
Bridge decks undergo continual stress from the traffic load they support and the environment to which they are exposed. Bridge deck inspections are conducted to identify signs of deterioration and fatigue.
Fatigue damage to reinforced concrete deck slabs of road bridges is common after as little as 20 years of service. Typically, much of this type of damage is the result of low concrete strength, inadequate detailing of rebars, and overloaded trucks.
Highway bridge decks are typically paved with asphalt or Portland cement concrete.
However, the overlay makes it more difficult to detect the subsurface deterioration during inspections, and the overlay can also become damaged due to debonding. In some regions, bridge deck pavement layers are subjected to continual abrasion and deterioration from traffic and environmental assaults from intense heat and sunlight, rain, freeze-thaw, and road salts.
All of which results in the bridge deck being acutely subject to deterioration.
Looking and Listening for Signs: Bridge Deck Inspections
A bridge deck is typically inspected visually for cracks and damage due to deterioration. Using traditional practices, bridge inspectors visually inspect a bridge, make a record of cracks and other types of damage, take photographs and notes, and then assign the bridge a health rating. Of course, these visual inspections cannot assess the internal integrity or any damage underneath the deck overlay. Only what is visible to the naked eye can be accurately assessed this way.
In addition to cracks and fractures, a visual inspection entails inspecting the bridge deck looking for potholes, cracks, spalling, and other signs of deterioration.
Additional methods are often employed during a bridge deck inspection, such as the use of acoustical techniques. This is a non-destructive technique that is typically done by utilizing a hammer or a chain drag to identify changes in sound pitch.
Acoustical testing such as this can detect delamination, as well as the separation of coating or the splitting of a structure into layers, for inspectors who have developed the requisite “ear” for such methods. However, this technique cannot be used to test bridge decks with asphalt overlays.
Another method sometimes used for inspecting bridge decks that do not have asphalt overlays is infrared/thermal imaging. This non-destructive technique examines changes in infrared radiation from the surface of concrete and indicates delamination. It is relatively fast and can even be carried out from a moving vehicle.
Similar to infrared/thermal imaging is the use of ground-penetrating radar, or GPR. A test that is
non-destructive, GPR uses electromagnetic radiation imaging of the subsurface of the concrete and detects changes such as cracks, voids, and delamination. Unlike a strictly visual inspection, GPR can provide reliable and objective quantitative data on the concrete’s integrity before any issues become severe.
Digging in for Additional Data: Coring and Chipping
Often performed after initial inspection warrants further investigation; these destructive techniques can potentially damage a bridge deck’s overall integrity.
However, coring can provide much more information about the “health” of the concrete structure. Coring is accomplished by using a drilled core that leaves a hole allowing access to the steel reinforcement underneath. This allows the inspector to assess any corrosion damage and the concrete’s chemical and mechanical properties.
As one engineering text noted,
“Concrete bridges should be tested if the bridge inspection reported doubts regarding the structural performance of the existing structure. The tests available range from the completely non-destructive to those where the concrete surface is slightly damaged, to partially destructive tests such as core tests and pullout and pull off tests, where the surface has to be repaired after the test.”
So, what type of damage is typically found during a bridge deck inspection?
Common types of bridge deck roadway damage include transverse cracks that run perpendicular to the pavement centerline, longitudinal cracks, potholes, delamination, and seepage. Transverse cracks typically occur more often than longitudinal ones and can start as a thin crack less than 0.5 mm in width – equal to a human hair – and less than 2 cm in depth.
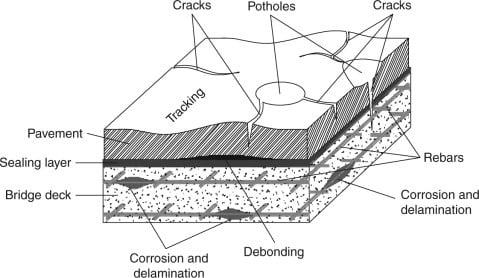
While damage to a bridge deck rarely, if ever, leads to a collapse of a bridge structure, it is only as strong as the components supporting it. And, in extreme conditions, it doesn’t take much to cause a failure.
In 1989, for example, the Loma-Prieta earthquake struck San Francisco. One of the structural casualties was the San Francisco-Oakland Bay Bridge. Although it only suffered four inches of movement during the tremor, a 76-by-50-foot section of the upper deck on the bridge’s eastern side fell onto the deck below.
Tragically, one person was killed, although the bridge was eventually repaired and, over the years, retrofitted.
For the Ideal Bridge Inspection Equipment, Look to McClain and Company
McClain and Company stands by our commitment to provide our customers with exceptional and knowledgeable service. This includes providing our customers with the best in under bridge and aerial access equipment rentals.
Daniel McClain, owner of McClain & Co., Inc., and his team also stand behind the belief that “your success is our success,” which is what motivates our mission to do all we can to help you select the right aerial access equipment rental for your project.
Feel free to talk with us about which type of equipment you’d like to rent. We’d be delighted to give you a quote and schedule your rental with us today.
At McClain and Company, we offer SNOOPER™ trucks as well as a wide variety of other under bridge inspection equipment rentals. In addition, we have a broad selection of Hi-Rail and aerial work platforms and access equipment, as well as professional highway construction services and equipment rental in several states, along with Traffic Control Service and Device rentals.
If you’d like to learn more about bucket truck rentals, SNOOPER™ trucks, or you just have some general questions concerning under bridge inspection units, feel free to contact us by calling 1.888.889.1284 or emailing us at [email protected].