The United States is home to over 618,400 highway bridges, according to the American Road & Transportation Builders Association (ARTBA) 2022 Bridge Report.
Along with regular cleaning, maintenance, and repair – in addition to periodic rehabilitation – these publicly owned bridges must be inspected routinely. How often highway bridge inspections occur, however, hinges on several factors.
Federal Bridge Safety Mandates and Highway Bridge Inspection Requirements
In 1971, the Federal Highway Administration (FHWA) adopted the National Bridge Inspection Standards (NBIS) regulations in response to the U.S. Congress enacting the Federal-Aid Highway Act of 1968. The NBIS directly resulted from the Silver Bridge collapse in Point Pleasant, WV, on December 15, 1967.
The NBIS applies to all structures defined as highway bridges on all public roads, on and off Federal-aid highways, including tribally and federally owned bridges. In addition, NBIS applies to private bridges that are connected to a public road on each end.
According to the NBIS, each bridge must be inspected at intervals not exceeding 24 months. However, the NBIS allows for extended intervals on certain bridges meeting all of the criteria recorded in the NBI (§ 650.315). These bridges may be inspected at intervals not to exceed 48 months.
The FHWA defines a “routine inspection” in the NBIS as,
“Regularly scheduled comprehensive inspection consisting of observations and measurements needed to determine the physical and functional condition of the bridge and identify changes from previously recorded conditions.”
In addition, a service inspection must be performed during the month midway between routine inspections when a risk-based, routine inspection interval exceeds 48 months. A “service inspection” is defined as,
“An inspection to identify major deficiencies and safety issues, performed by personnel with general knowledge of bridge maintenance or bridge inspection.”
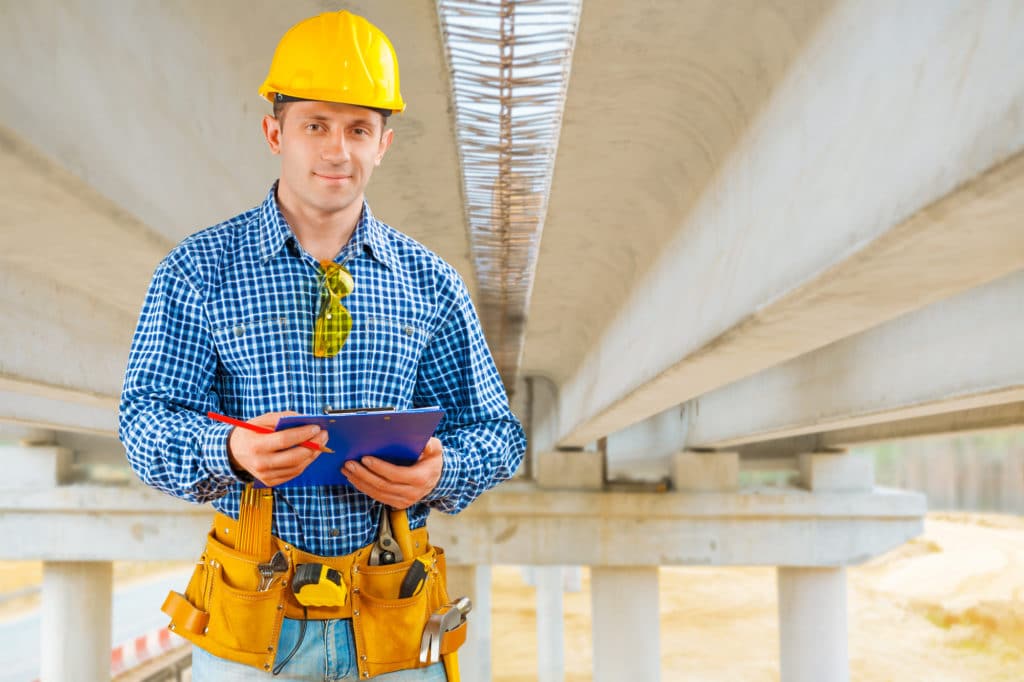
NBIS, Bridge Inspections, and Recent Updates
On June 6, 2022, a final rule submitted by FHWA addressing bridge inspections officially went into effect, making changes to the National Bridge Inspection Standards. The NBIS was last updated more than a decade ago.
The recent final rule published in the Federal Register resulted from a requirement of the Moving Ahead for Progress in the 21st Century Act (MAP-21) mandating the U.S. Department of Transportation to update the National Bridge Inspection Standards.
According to a recent article from Land Line Media,
“Provisions within MAP-21 include new requirements for:
- The highway bridge inspection program.
- Maintaining a bridge inventory.
- Reporting to FHWA the inspection results and critical findings (“critical findings” include any structural or safety-related deficiencies that require immediate follow-up inspection or action).
New rules include ‘options for more rigorous, risk-based intervals based on the consideration of certain factors,’ including an inspection interval tolerance of three months beyond the inspection date. Specific criteria allow for extended routine inspection intervals up to 48 months, and 72 months for underwater inspections.”
Congress stated in the MAP-21 Act that inventorying, inspecting, and improving the condition of highway bridges is in the nation’s best interests.
Standard Types of Highway Bridge Inspections
Government agencies such as state DOTs can conduct bridge inspections whenever they deem it appropriate or needful. However, there are a series of designated types of standard highway bridge inspections that are either required or carried out on an as-needed basis.
The six different types of inspections and their definitions are as follows:
Damage inspection
An unscheduled inspection assesses structural damage resulting from environmental factors or human actions.
In-depth inspection
A close-up, detailed inspection of one or more bridge members located above or below water, using visual or nondestructive evaluation techniques as required to identify any deficiencies not readily detectable using routine inspection procedures. Hands-on inspection may be necessary at some locations, and in-depth assessments may occur more or less frequently than regular inspections, as outlined in bridge-specific inspection procedures.
Initial inspection
The first inspection of a new, replaced, or rehabilitated bridge. These inspection records required bridge inventory data, established baseline conditions, and set intervals for other inspection types.
Routine inspection
Regularly scheduled comprehensive inspection consisting of observations and measurements needed to determine the physical and functional condition of the bridge and identify changes from previously recorded conditions.
Service inspection
An inspection to identify significant deficiencies and safety issues, performed by personnel with general knowledge of bridge maintenance or bridge inspection.
Special inspection
An inspection scheduled at the discretion of the bridge owner is used to monitor a particular known or suspected deficiency or to monitor unique details or unusual characteristics of a bridge that does not necessarily have defects.
Each state is ultimately responsible for inspecting all public highway bridges within the State, except for those federally or tribally owned, according to the Federal Highway Administration.
The FHWA goes on to state that,
“The State may delegate bridge inspection policies and procedures, quality assurance and quality control, preparation and maintenance of a bridge inventory, bridge inspections, reports, load ratings, and other standards requirements to smaller units of the State like a city or county.”
These entities may, in turn, rely on private contractors to conduct inspections on their behalf.
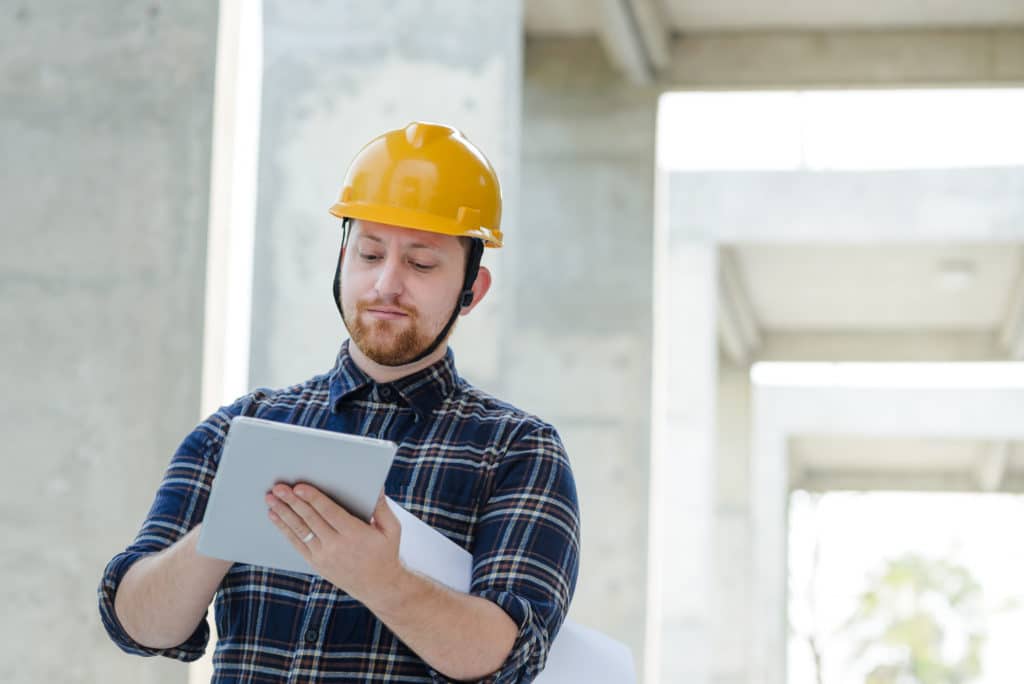
Routine Highway Bridge Inspections Require Specialized Under Bridge Access Equipment
With more than 600,000 highway bridges being inspected at least once every two years, it’s reasonable to assume that hundreds of bridge inspections occur across the country every day.
Some of these inspections can be achieved with smaller vehicles such as utility bucket lifts or other aerial lift equipment. However, most bridges require underbridge access that cannot be achieved from the ground.
And that’s when a reliable method for providing under-bridge access is necessary.
Traditionally, equipment ranging from suspended scaffolding structures to rope climbers and rope rigging have been utilized to access the areas underneath highway bridge decks. But since the advent of specialized vehicles such as the first Paxton-Mitchell SNOOPER® truck in 1964, the safety and superior accessibility provided by under-bridge inspection vehicles have largely replaced these older methods.
Since the primary purpose of routine inspections is to “determine the physical and functional condition of the bridge,” it is necessary for an inspector to have close access to every area of the bridge.
Inspecting the bridge deck is usually easy enough without access equipment. However, some highway bridges have overarching superstructures that may not be accessible by foot, especially with older structures like highway truss bridges.
But the most common challenge on almost every highway bridge higher than 30 feet above the ground, or those that span waterways and active roadways, is accessing the areas underneath the bridge deck.
This means seeing and having “hands on” access to the bridge substructure, including all the critical components such as abutments, piers or columns, caps, girders, beams, and bearing. This can be achieved by using a suitable under bridge access vehicle, of which there are many types and sizes.
Any agency or contractor tasked with highway bridge inspections knows that the cost of purchasing just one under bridge access vehicle can easily run into the tens of thousands of dollars – or more. And because the accessibility requirements of different bridge structures can mean different types of under bridge access equipment is needed, that can mean they need more than one vehicle.
Very few entities engaged in bridge work have the resources to buy and maintain their own fleet of under bridge access equipment, which is why it makes much more sense economically and logistically to rent the particular equipment needed.
McClain and Company should be your number one choice for equipment rentals.
McClain & Co., Inc. Is Your Number One Source for Bridge Inspection Equipment Rentals
At McClain and Company, we have dedicated the last two decades providing quality support services to government agencies and engineering companies for inspecting and maintaining highway and railroad bridges throughout the United States. And we have always been dedicated to providing our customers with exceptional customer service.
“Your success is our success.”
This is what we believe and what owner Daniel McClain and the team at McClain & Co., Inc. hold up as our mission. And we achieve this by doing all we can to help you succeed with your projects. This mission includes helping you select the right equipment rental for your bridge inspection or bridge maintenance and repair project.
If you have a bridge inspection project lined up and know which piece of equipment you’d like to rent, you can request a quote today and schedule your rental with us.
In addition to our reliable and high-quality bridge inspection equipment rentals, the professionals at McClain and Company also provide Hi-Rail UBITs and bucket trucks, specialty aerial work platforms, and other access equipment. We also provide our customers with various construction services, construction equipment rentals in several states, and Traffic Control Service and Device rentals.
Suppose you have questions about our bridge inspection equipment and other rental equipment or want to learn more about our other services. In that case, you can contact McClain and Company by simply calling us at 1.888.889.1284 or emailing us at [email protected].